Projet réalisé dans le cadre du Consortium industriel FactoryLab avec les expertises du CEA-List, du CETIM et de IQANTO (PREDICT), en collaboration avec les industriels Safran, Naval Group, Stellantis et SLB.

Contexte
Les équipements de soudage et les nouvelles générations de capteurs permettent une remontée d’informations exhaustive singulière de la physique du procédé. Or, ces données sont actuellement peu ou pas exploitées.
Enjeux & innovation
L’enjeu du projet RACOSOUD était de parvenir, à partir du traitement de ces données, à identifier des indicateurs signalant un défaut de soudure de manière inéquivoque ou d’émettre un signalement afin de procéder à un contrôle particulier ultérieur.
L’enjeu industriel vis à vis de ce procédé de soudage par résistance par point est important puisque le suivi qualité par des approches classiques (contrôle non destructif par exemple) de ce type d’assemblage reste difficile. A ce propos, le projet a également intégré un volet développement de contrôle non destructif par ultrasons multi-éléments performant qui complète les travaux concernant l’exploitation des données.
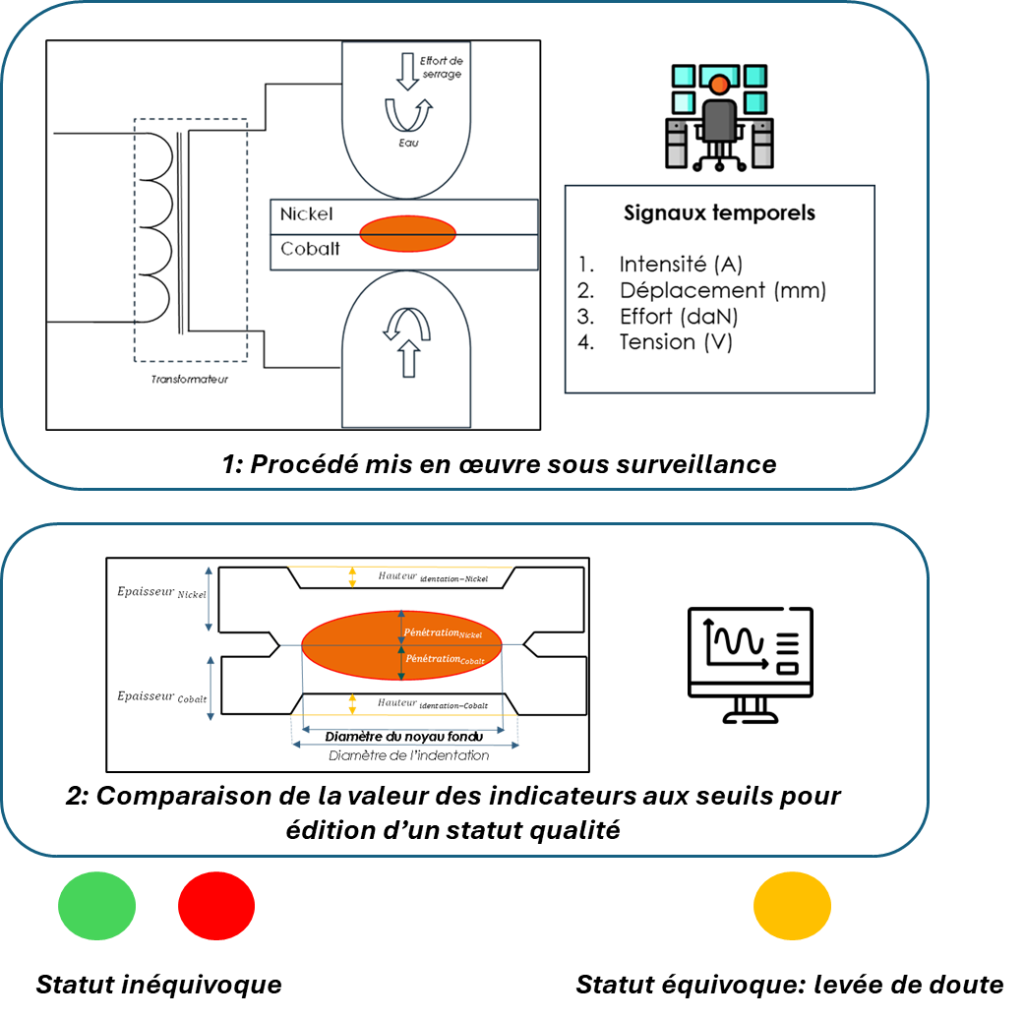
Pour le projet RACOSOUD, IQANTO a mis en œuvre sa solution numérique KASEM® couplées à des technologies d’IA dans 3 stratégies de surveillance pour établir des liens de corrélation/causalité entre les données process (Intensité, Tension, Effort, Déplacement, …) et la qualité de la soudure obtenue.
Stratégie N°1 : Etablissement du lien entre les signaux temporels et la qualité du point soudé.
Stratégie N°2 : Approche IA pour établir le lien entre les indicateurs calculés par la Stratégie N°1 et la qualité du point soudé.
Stratégie N°3 : Etablissement du lien entre la consigne et la qualité du point soudé.
Résultats
Dans le cadre du projet, un équipement de soudage par résistance mis en œuvre par SAFRAN Helicopter Engines a été instrumenté de capteurs permettant l’enregistrement de données physiques jugées pertinentes en vue de caractériser la qualité des assemblages réalisés.
Un plan d’expérience a permis d’établir les corrélations entre les grandeurs physiques et la qualité des assemblages.
Ce projet et les résultats obtenus dénotent de la littérature scientifique traitant de la prédiction de la qualité d’un assemblage par analyse des enregistrements issus du soudage sur les aspects suivants :
- Le plan d’expérience a intégré l’impact de l’ensemble des facteurs influents sur la qualité obtenue en soudage, en intégrant en particulier les conditions d’usure de certains composants, l’état de surface des tôles soudées, etc. ; en effet, la plupart des publications n’intègrent dans leur cas d’étude que l’impact des consignes « procédés » (variations des consignes opératoires sur le générateur de soudage);
- L’étude a été mise en œuvre sur des matériaux dits « aéronautiques » (base nickel et cobalt), alors qu’usuellement l’étude porte sur des aciers non alliés ;
- L’approche pour le traitement des données a intégré trois étapes :
- Une première analyse « humaine » de la donnée visant à établir des corrélations simples entre la donnée enregistrée et la qualité des points soudés ;
- Un deuxième traitement « automatisé », par le biais d’outils issus de l’intelligence artificielle, établissant des corrélations plus complexes entre la donnée et la qualité ;
- Une comparaison critique des deux traitements obtenus et l’établissement final des indicateurs de suivi de la qualité des points soudés.
On présente ci-dessous un tableau de synthèse des différentes stratégies pouvant être mises en œuvre pour suivre la qualité des points soudés par résistance. Le code couleur indique le niveau de robustesse de l’indicateur obtenu à ce jour.

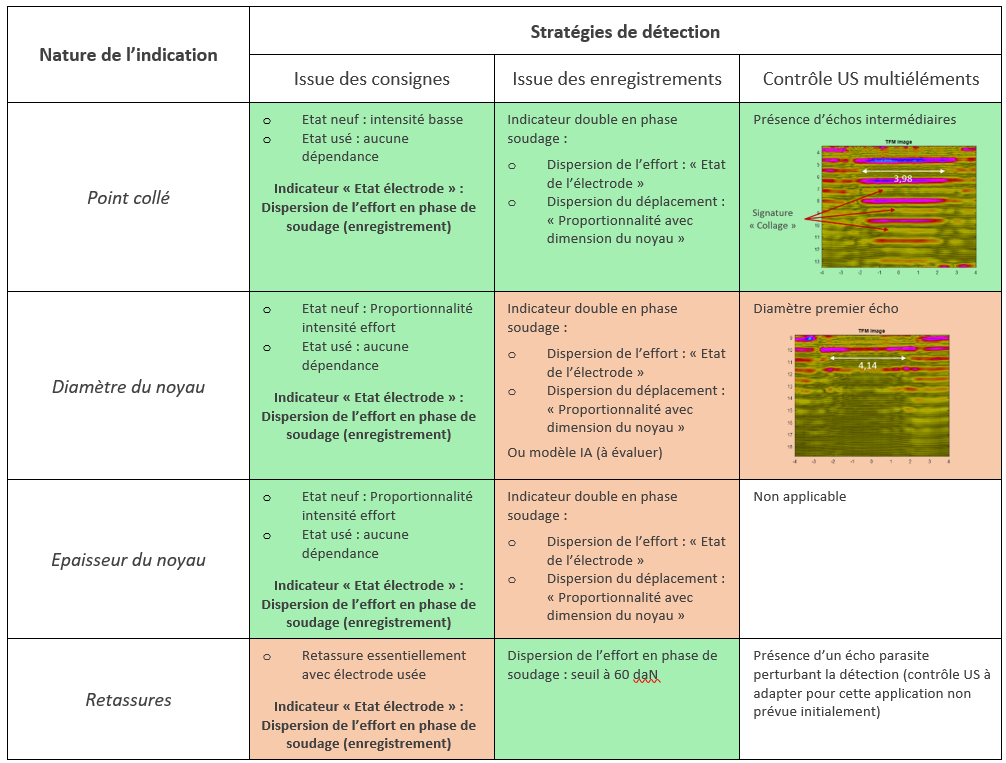
Le projet aura également permis de poursuivre le développement d’une solution performante de contrôle non destructif des points soudés par résistance (US multi éléments) qui est une solution complémentaire à la prédiction de la qualité des assemblages par surveillance des données procédés. Le contrôle US multiéléments a pour vocation de sanctionner définitivement la qualité d’un point soudé par résistance lorsqu’un doute a été levé par la surveillance des paramètres. Ce contrôle a permis la mise en évidence de la bonne détection de points « collés ». Concernant l’évaluation des diamètres des points soudés, l’étude montre des résultats encourageant quoique pas totalement satisfaisant en raison d’un état de surface de points soudés dégradés et pas forcément représentatifs. Enfin, sur le cas des retassures, le capteur utilisé n’était pas adapté car ce point ne faisait pas l’objet de l’étude définie initialement.
Parmi les résultats obtenus avec les technologies mises en œuvre par IQANTO, il est à noter :
- La détection d’un changement de comportement de l’intensité avec confirmation que les écarts constatés sont dus à un problème de calibration de capteurs;
- La détection d’une dérive lente à la hausse de la dispersion du déplacement de l’électrode de soudage permettant d’envisager le suivi de l’usure des électrodes.
Conclusions
Le projet a permis d’exploiter de nombreuses grandeurs physiques (effort, déplacement, courant et tension) sous différentes formes (médiane, dispersion, intégrale, …) afin d’identifier des liens de corrélations complexes avec la qualité des points soudés par résistance.
Ce travail a permis d’aboutir à l’établissement de différents indicateurs de suivi de la qualité de la soudure qu’il reste à éprouver dans un environnement de production hors plan d’expérience.
Perspectives
Il s’agit à présent de poursuivre l’évaluation de la pertinence des indicateurs établis dans un environnement de production (hors périmètre du plan d’expérience) afin d’industrialiser ensuite la solution.
C’est avec cet objectif que SAFRAN Helicopter Engines et IQANTO poursuivent leur collaboration afin de rendre robustes les indicateurs de surveillance élaborés au cours de cette première phase. Pour se faire, les données de production de plusieurs dizaines de lots de pièces soudées seront collectées, traitées et analysées afin d’améliorer la détection précoce d’anormalités de soudage et d’envisager des indicateurs prédictifs de non-conformité de points soudés.
Auteurs : Samuel CRETIN (CETIM), Hugues LOURME (CEA-List), Florent BARBIER (IQANTO).