Projet réalisé dans le cadre du Consortium industriel FactoryLab, mené par le CETIM avec l’appui de R&D Vision et en collaboration avec Naval Group, Stellantis, SLB et Safran.

Pouvoir détecter au plus tôt les défauts de soudage débouchants et sous-jacents pour éviter les reprises (post-process) couteuses en coûts et en qualité
Dans un contexte réglementaire fort, les professionnels qui mettent en œuvre les procédés de soudage ont besoin d’améliorer les performances et la productivité des contrôles afin de rester compétitif dans un marché fortement concurrentiel. Par conséquent, la recherche de solutions innovantes et performantes levant des verrous technologiques représente dans ce contexte un véritable enjeu.
Traditionnellement le contrôle de la qualité des soudures peut être réalisé soit en cours de soudage (entre passes) via des méthodes surfaciques (ressuage, magnétoscopie), soit après soudage via des méthodes surfaciques et volumiques (radiographie, ultrasons). Ces types de contrôle impliquent des réparations lourdes en cas de non-conformités.
Un contrôle non destructif des soudures pendant le process de soudage (surveillance en ligne) permettrait de réduire voir de s’affranchir des contrôles traditionnels en détectant de manière précoce l’apparition de défauts, et ainsi gagner du temps dans la phase de réparation ou de mise au point de nouveaux procédés de soudage. Le cas d’application, Safran, traité dans le cadre du projet QUALISOUD a été le procédé de soudage TIG sur des éprouvettes à bords droits en inconel d’1mm d’épaisseur soudées bout à bout.
Déterminer la configuration adéquate à une bonne visualisation de la scène de soudage
La première chose dans ce type d’étude est d’obtenir une bonne netteté du bain de fusion et/ou du cordon en cours de refroidissement (zone de solidification et de refroidissement). En effet, cette étape est primordiale pour la suite de l’étude et, après une grande quantité d’essais avec de nombreux réglages, la réduction de la saturation des rayonnements émis par l’arc sur le détecteur a pu aboutir permettant une bonne visualisation du bain de fusion et du cordon se refroidissant.
Création et détection des défauts les plus courants/nocifs dans ce type d’assemblage
Ensuite, il faut bien entendu pouvoir créer les défauts souhaités à la demande, les défauts qui ont été choisi les plus représentatifs (courants/nocifs) sont les manques de fusion, les inclusions, les fissures et les manques de pénétration. Ces défauts ont pu être générés en jouant sur les variables de soudage, leur détection a été confirmé :
- Soit par lecture seule du thermogramme pendant l’acquisition et la confirmation de détection par une autre méthode de contrôle non destructive et/ou destructive;
- Soit à postériori, après la détection par une autre méthode de contrôle non destructive et/ou destructive d’une indication sur l’éprouvette et la confirmation de sa présence sur le thermogramme et/ou de sa détection avec des données brutes.
Répétabilité de détection des défauts
Afin de tester cette nouvelle technologie, une phase de répétabilité de détection des 4 défauts cités a été entreprise. Les manques de fusion, inclusions et fissures ont pu être reproduis de nombreuses fois et leur taux de détection par thermographie infrarouge se situe à plus de 90%. En ce qui concerne le manque de pénétration, tout d’abord il est peu courant sur ce type d’assemblage, de plus sa création n’a pas été chose aisée car il produisait également en parallèle des manques de fusions, enfin l’assemblage étant bout à bout, le côté envers est l’air libre, donc il n’y a que très peu de flux radiatifs emmagasinés dans le manque de pénétration et peu de possibilité de détection.
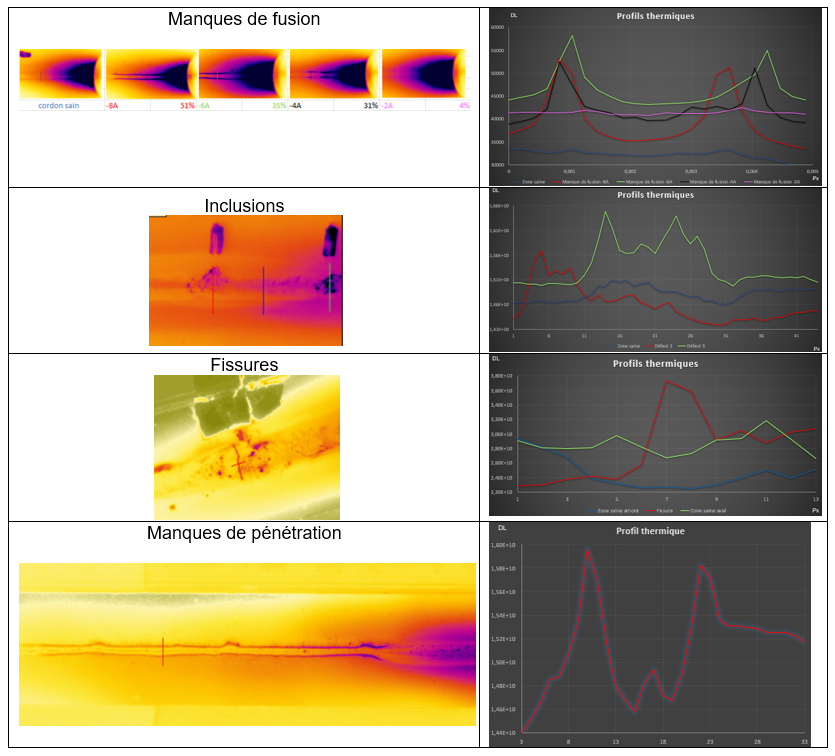
Crédits photos : Cetim
On a pu se rendre compte que dans la majorité des essais réalisés, un défaut engendre à minima :
- Un gradient de flux radiatif;
- Une signature thermique;
- Et/ou un décalage spatial.
Les évolutions de densité de flux radiatifs dû aux défauts ainsi que leurs données brutes respectives nous permettent d’entrevoir la possibilité de détection automatique.
Traitement et détection automatique des défauts
R&D Vision a donc travaillé sur la possibilité de détecter automatiquement certains défauts dans les images issues des thermogrammes. L’objectif exprimé par les industriels est de pouvoir surveiller en temps-réel le procédé de soudage et d’alerter voire localiser la présence d’anomalie dans le cordon. Deux types d’anomalies ont été traités en priorité, à savoir le manque de fusion et les fissures. Les signatures visuelles sont significatives, reproduites avec succès lors des phases expérimentales, elles sont corrélées par des méthodes de référence CND.
En fonction de l’emplacement dans l’image, le niveau d’intensité est très variable. Le soudage TIG génère un effet de saturation important au niveau du bain de fusion (à proximité de la torche). Une première étape du traitement a été d’étudier et de choisir judicieusement la zone de l’image avec la meilleure dynamique à exploiter. Plusieurs méthodes de filtrage ont ensuite été testées et validées pour s’affranchir d’un bruit de fond variable.
Sur la base de plusieurs enregistrements vidéos, R&D Vision a développé une méthode de détection automatique sur la base d’un filtrage adaptatif permettant d’extraire et retrouver la signature de chacun des défauts. Ce prototype algorithmique est une première étape qui ouvre des perspectives sur la capacité à détecter des défauts dans les procédés de soudage grâce à la thermographie infrarouge.
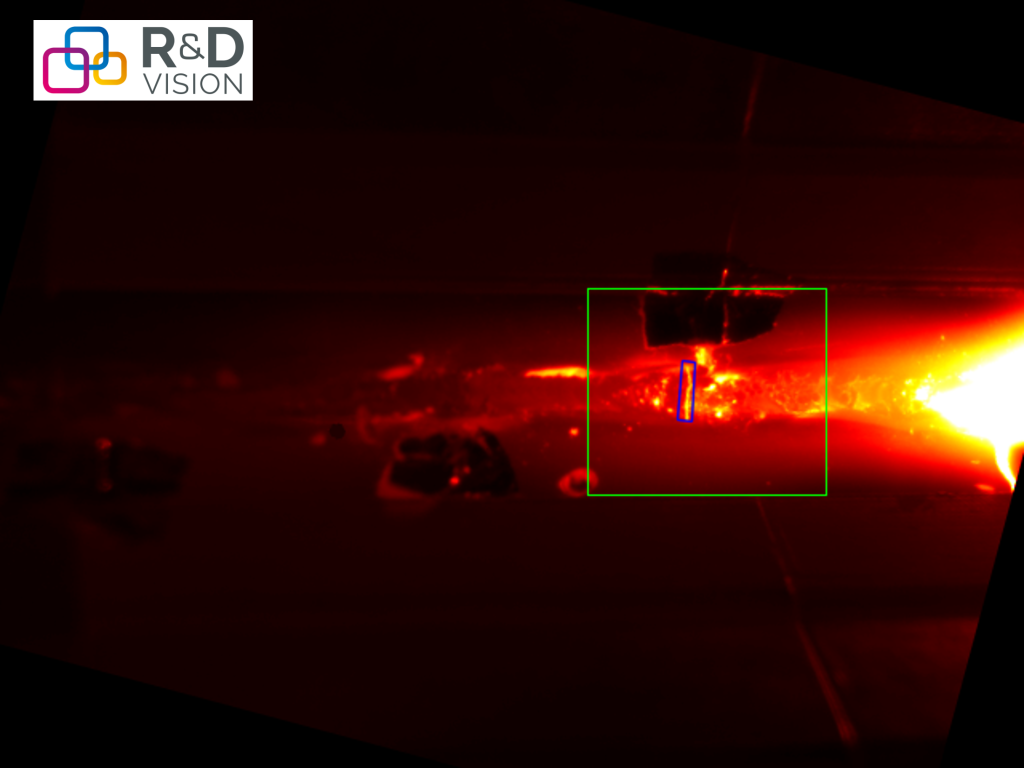
Crédit photo : R&D Vision
Instrumentation de la thermographie infrarouge en milieu industriel
L’intégration du matériel de thermographie par le CETIM à la production SLB a pu montrer la robustesse de l’instrumentation des caméras de laboratoires en notre possession en conditions industrielles.
Conclusion et perspectives
Toutes les phases du projet ont pu être menées à bien, que ce soit la visualisation des scènes de soudage, la création et détection des discontinuités recherchées, la répétabilité de détection ainsi que les possibilités de détection automatique et d’instrumentation.
Tout au long du projet, des pistes d’améliorations techniques, matérielles et logicielles ont été identifiées, à savoir le dimensionnement des indications (plus petit défaut détectable), le choix d’une caméra peu encombrante, un logiciel qui permet l’acquisition, l’analyse et la sanction, la corrélation des paramètres de soudage ou encore les problématiques éventuelles de réparations à chaud.
Auteur : Sébastien SAINT YVES, chef de projet QUALISOUD, CETIM et Laetitia LAVANCIER, Responsable Grands Comptes, R&D Vision.