Projet réalisé dans le cadre du Consortium industriel FactoryLab avec les expertises croisées du CEA-List, du CETIM et de l’ENSAM-Paris en collaboration avec Isybot, Naval Group, Stellantis et Safran.

Des machines guidées manuellement, des manipulateurs aux cobots
Les manipulateurs industriels sont des machines qui permettent aux opérateur des déplacer des charges sans les porter. Distincts des robots manipulateurs, ils sont catégorisés comme appareils de levage[1]. Quand ils intègrent des fonctions issues de la robotique comme des guides virtuels ou des limitations logicielles de l’espace de travail, on parle de cobots ou IAD (Intelligent Assist Devices).
En robotique industrielle, le mode de guidage manuel permet de faciliter l’apprentissage de points en programmation; il peut aussi être utilisé dans des applications d’assistance au port de charge. Le terme de cobot s’est imposé également pour les robots qui offrent ce type de fonctions. Dans le cadre du thème « Assistance Physique à l’Opérateur », le consortium FactoryLab soutient le développement de technologies innovantes qui répondent à des besoins industriels pour lesquels les moyens existants d’assistance physique ne sont pas satisfaisants : assemblage de grandes pièces en aéronautique (projet MANIPRES) , travail avec des outils sur des postes encombrés (projet BAR10).
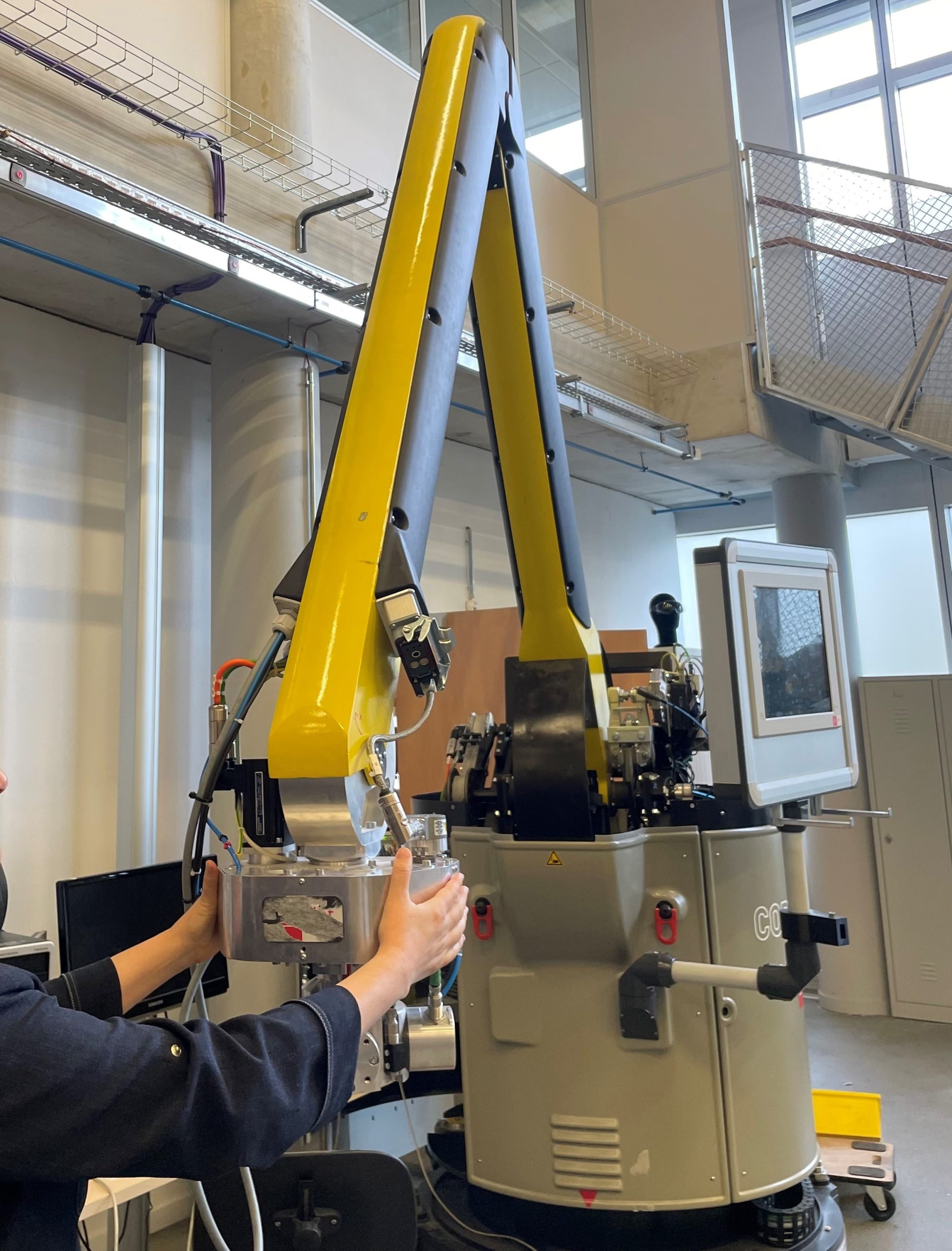
fonctions d’assistances
Crédit photo : CEA-List
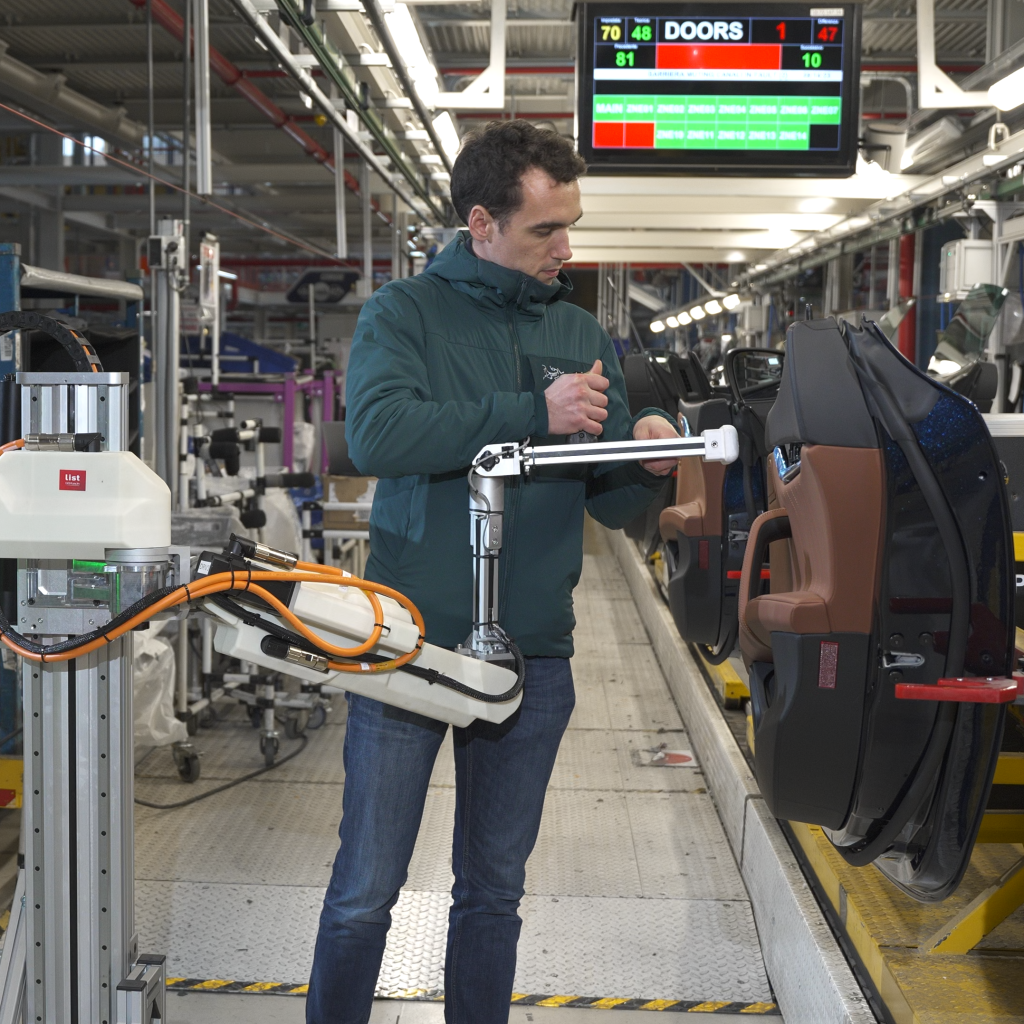
Crédit photo : CEA-List
Des moyens d’assistance réellement utilisables
Les manipulateurs industriels sont couramment implantés dans des usines où ils se trouvent sous-utilisés, particulièrement quand il s’agit de charges moyennes d’une dizaine de kg : Quand la charge reste transportable manuellement les opérateurs peuvent préférer travailler sans une assistance qui gêne ou ralenti, même si cela se fait au détriment de leur santé et de leur sécurité. Cette problématique concerne de nombreux postes chez nos industriels utilisateurs pour lesquels les charges manipulées de façon répétitives sont sources de TMS (troubles musculosquelettiques) et de difficultés de maintien au poste.
Un des facteurs de cette sous-utilisation est « mécanique » : Ces systèmes reprennent la charge (le poids de l’objet à transporter) mais peuvent demander des efforts importants dans la mise en mouvement ainsi que dans le contrôle de ce mouvement.
Pour objectiver cette difficulté, les ergonomes peuvent relever au dynamomètre le niveau des forces et prescrire un niveau à ne pas dépasser[2]. Ces mesures ne traduisent que de façon incomplète[3] la difficulté de contrôle du mouvement et ne peuvent être réalisées qu’à postériori.
En phase de conception d’un poste de travail, se posent des questions de faisabilité et de dimensionnement du moyen d’assistance : Est-ce qu’une assistance qui compense la gravité peut permettre de respecter les seuils ergonomiques ? Comment spécifier la performance du moyen d’assistance pour ne pas dépasser ces seuils ?
Dans le cas de robots collaboratifs, à l’heure actuelle, les constructeurs de robots ne donnent pas de caractéristiques de performance de leurs modes de guidage manuel et les comparaisons restent subjectives[4].
Modélisation et mesure de la transparence mécanique
Un modèle élémentaire mais informatif
La notion de transparence a été introduite pour la télé-opération à retour d’effort[5] : Il s’agit pour l’opérateur de ressentir l’objet manipulé ou l’environnement touché par l’effecteur comme s’il interagissait directement. Dans le cas d’une assistance au port de charge ou du guidage manuel d’un robot, cet idéal de transparence deviendrait celui de n’appliquer aucun effort tout en conservant une capacité de contrôle des mouvements de la charge.
Le comportement du système que l’on cherche à caractériser est un comportement mécanique externe, vu de sa prise par l’opérateur. La notion d’impédance[6] mécanique permet de définir comment un système résiste au mouvement. Bien que complexe, ce comportement peut être caractérisé de façon locale pour une configuration donnée et selon une direction.
Pour les systèmes qui nous intéressent, un modèle physique simple permet le plus souvent de décrire l’impédance. Il est composé d’une masse apparente et de deux composantes de frottement visqueux et statique.
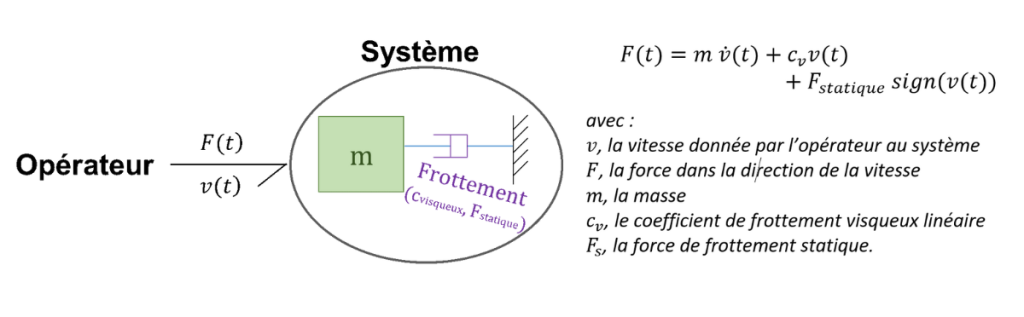
Ce modèle permet de prédire les efforts dans la direction du mouvement désiré à condition de connaître le profil temporel de la vitesse et de l’accélération. Comment connaître à priori ce profil lors de la spécification d’un moyen d’assistance ? Dans un mouvement naturel du bras, il a été montré[7] que la trajectoire suit une trajectoire minimisant le jerk (dérivée temporelle de l’accélération). A partir de cette propriété nous construisons une trajectoire type qui correspond à un déplacement dont la longueur et la durée sont prescrites[8]. Cette trajectoire ne traduit pas la variabilité interindividuelle mais traduit l’effet des contraintes de la tâche sur les vitesses et accélérations requises. A partir de la trajectoire type, des abaques peuvent être construite pour définir quels sont les paramètres du modèle d’impédance qui permettront de respecter des limites de forces ergonomiques.
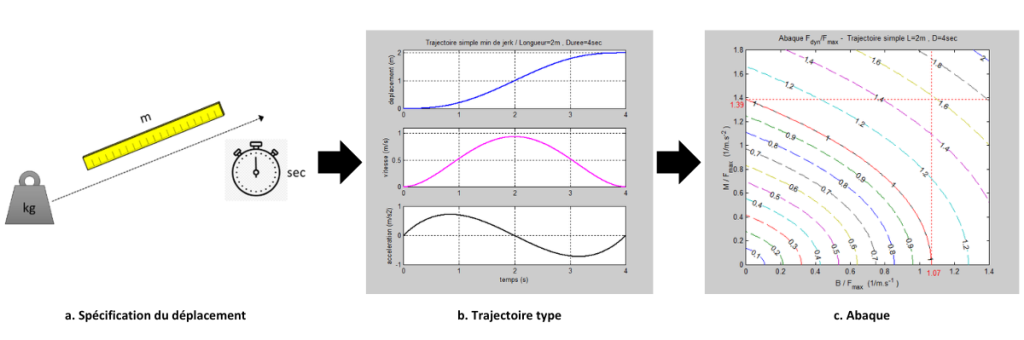
Des dispositifs de mesure
Nous proposons de mettre en œuvre un moyen externe qui va solliciter le système en mouvement et mesurer les efforts de réaction. La sollicitation est réalisée en translation selon une direction. L’effort mesuré est l’effort d’interaction.
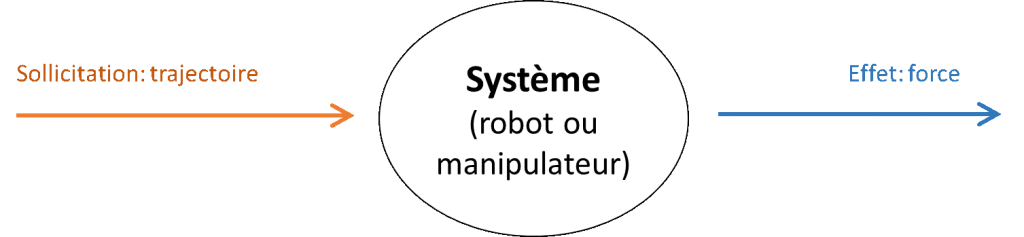
Trois systèmes de mesure externe ont été proposés. Les deux premiers imposent un mouvement rectiligne par un rail linéaire ; dans le troisième le mouvement n’est pas contraint :
- Le premier est motorisé et permet d’imposer des trajectoires d’excitation. Le mouvement est mesuré par le codeur moteur;
- Avec le second dispositif, le mouvement est imposé manuellement le long du rail et mesuré par un codeur linéaire magnétique;
- Le troisième est mobile et le mouvement donné par l’opérateur est mesuré par une centrale inertielle.
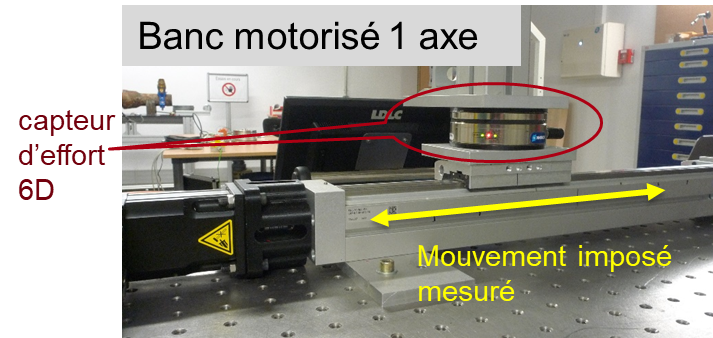
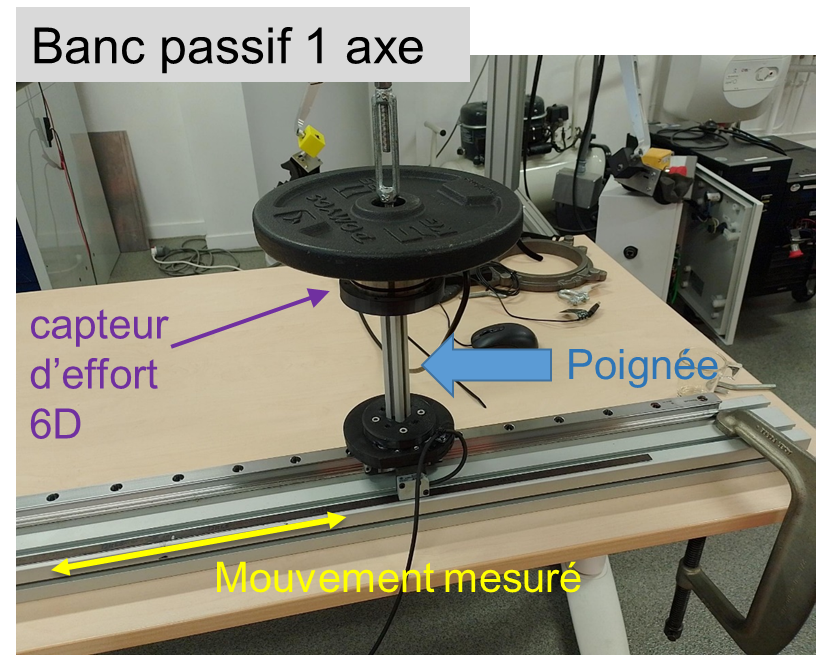
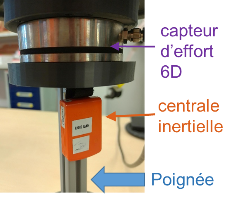
Figure 4 : Les trois dispositifs de mesure prototypes
Crédits photos : CEA-List
Nous avons utilisé un capteur d’effort 6-axes pour évaluer non seulement l’effort dans la direction du mouvement, mais aussi les efforts latéraux.
Dans le cas du dispositif motorisé nous utilisons des trajectoires de différents types : paliers de vitesses qui permettent d’identifier séparément le modèle de frottement, sinus vobulés et trajectoires à minimum de jerk. Dans le cas des dispositifs activés manuellement, on recommande de combiner des essais avec des trajectoires naturellement adoptées par l’opérateur et des essais excitants[9].
Les données mesurées sont filtrées[10] et le modèle simple est identifiable par moindre carrés. Des indicateurs sont calculés pour définir la qualité de l’identification (identifiabilité des paramètres et écart entre mesure et modèle). Dans les essais manuels, on combine des essais avec des trajectoires de nature différentes pour obtenir une identification robuste.
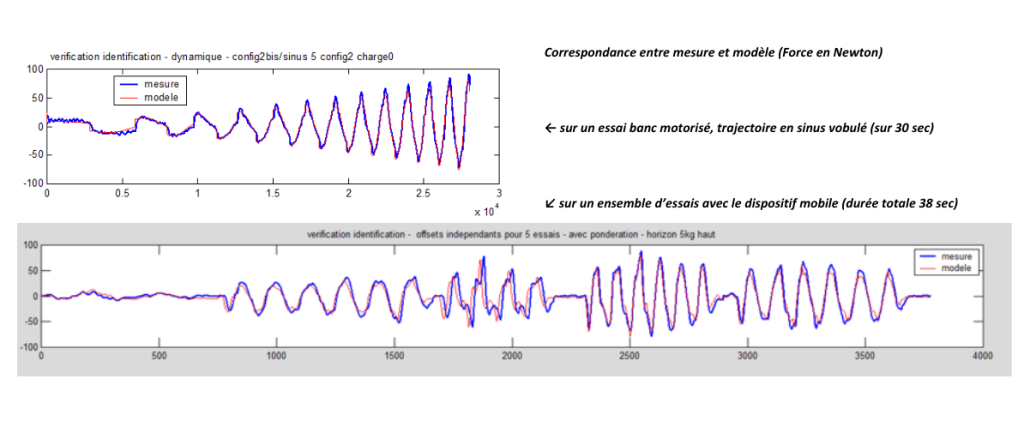
Test pratique des moyens de mesure
Identification d’un modèle physique
Un modèle est identifié qui relie la force et le mouvement dans la direction du mouvement. Nous avons pu tester l’identification sur 5 systèmes différents :
- Deux robots « collaboratifs » , l’un avec actionneurs à câbles et vis à bille, l’autre avec actionneurs classiques (à engrenages[11]);
- Deux solutions de manutention industrielle : un manipulateur de charges avec fonctions d’assistance actives, un portique avec chariot et pont roulant;
- Un bras d’assistance au port d’outil, articulé et passif (équilibré par ressort).
A partir de ces essais dont l’objectif premier était de valider le moyen de mesure et l’identification, nous avons pu voir que les systèmes peuvent être catégorisés selon les valeurs des paramètres obtenus et leur influence relative : un comportement inertiel (masse dominante) pour le manipulateur industriel et le portique de manutention. Un comportement très visqueux (coefficient dominant) pour le robot collaboratif à actionneurs classiques.
Considérations sur la pratique des essais
La configuration de mesure est définie par :
- La charge[12];
- La direction du mouvement;
- L’orientation de l’effecteur;
- La configuration des axes dans le cas d’un système articulé[13];
- Et pour les systèmes actifs, la configuration du contrôle[14].
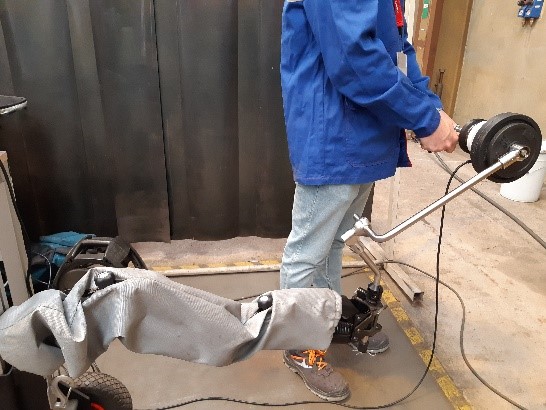
Crédit photo : Naval Group
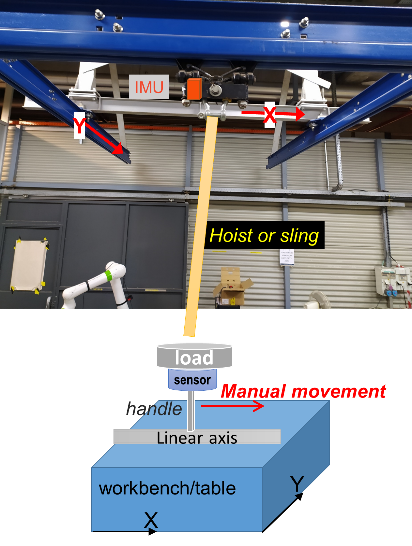
Crédit photo : CEA-List
Dans le cas d’une mesure avec rail, la position fixe du rail contraint la configuration d’essai, mais dans le cas du système de mesure mobile, cette configuration peut facilement varier lors de la répétition des essais. Il convient alors de prendre des repères (visuels et/ou matériel) pour conserver une même configuration quand on répète les tests[15].
Mis à part le cas du portique, le modèle simple à une masse permet d’estimer la force.
Dans le cas du portique, le modèle simple à une masse n’est pas adapté et un modèle à deux masses a été adopté[16]. Son identification est plus complexe : il est possible d’identifier un modèle fréquentiel à condition d’effectuer des sollicitations très excitantes. Nous avons opté pour une sollicitation manuelle avec une mesure supplémentaire : le mouvement du chariot qui correspond à la seconde masse était observé par une centrale inertielle (voir Figure 7).
L’importance des efforts latéraux
L’importance de l’effort latéral traduit une difficulté de contrôle précis du mouvement dans une direction imposée par l’opérateur. Les efforts latéraux ont été mesurés lors de essais et nous avons proposé des critères qui traduisent la proportion entre la force latérale et celle dans la direction du mouvement.
Dans les essais effectués avec un rail les efforts latéraux sont repris par le rail et ne sont pas imposés par l’opérateur pendant le test. Nous avons observé des amplitudes importantes, même pour des systèmes qui qualitativement sont faciles à mettre en mouvement.
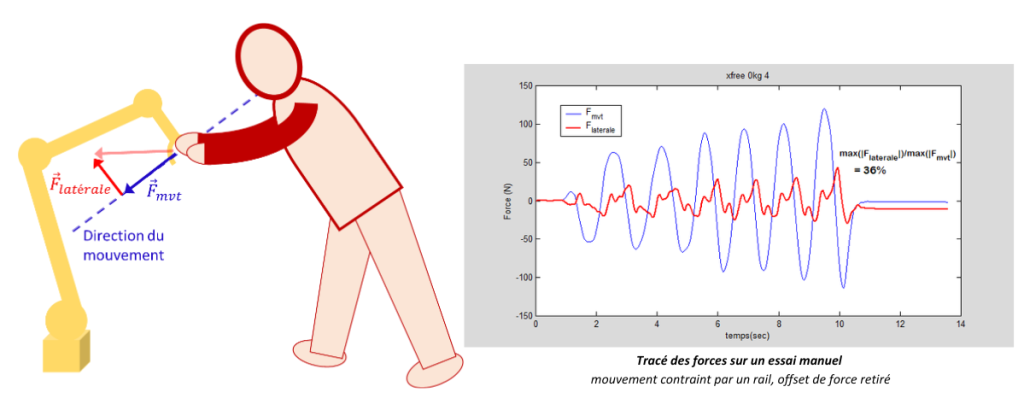
Dans le cas d’un robot collaboratif « classique », les efforts internes générés par la contrainte du rail fixe sont importants, ce qui nécessite un montage d’essai résistant. Ces essais activent fortement les flexibilités internes au robot et celle résiduelles du montage d’essai, ce qui n’est pas le cas lors de l’utilisation « naturelle » du robot. La question de la spécification des conditions de rigidité du montage reste ouverte.
Dans le cas d’essais avec le système mobile, c’est la rigidité de l’opérateur qui détermine le niveau des forces latérales. Les conditions d’essais sont donc plus naturelles mais sujettes à la variabilité interpersonnelle.
Plutôt que mesurer l’effort de résistance du système qui «préfère» une autre direction de mouvement, il est possible de mesurer la déviation de mouvement du système soumis à une force pure[17],[18]. Ce critère peut être plus répétable physiquement mais demande de mesurer assez précisément la position dans l’espace[19],[20].
Pour conclure
Définir et utiliser des critères de transparence mécanique
Pour un même système le niveau d’effort peut varier beaucoup selon le niveau de vitesse et d’accélération requis pour effectuer le mouvement. C’est le cas des force définies dans la norme d’ergonomie NF X35-109[21]. La caractérisation par les 3 paramètres du modèle d’impédance (voir Figure 1) est plus générale et elle permet de prédire le niveau de force que l’opérateur doit appliquer au système pour le déplacer en un temps donné.
Une des limites de la caractérisation est son caractère local. La dépendance à la configuration et à la direction peut être anticipée en fonction de la structure du système. Dans le cas le plus complexe des robots articulés, on pourra choisir des configurations et des directions sur le cube de le norme ISO9383. Le choix des configurations d’essai peut aussi être défini en fonction de la tâche à réaliser.
La difficulté de contrôle fin du mouvement, une question encore ouverte
Plus difficile est la caractérisation de la facilité ou difficulté de contrôle fin du mouvement.
Les forces latérales, i.e. l’effort pour maintenir la trajectoire sur une ligne précise, sont une des composantes de la difficulté de contrôle. Nous les avons mesurées mais elles sont difficilement prédites par un modèle simple. Les critères associés à cette mesure, que ce soit le rapport entre force latérale et force alignée au mouvement, ou l’angle entre la force appliquée et le mouvement résultant, dépendent fortement de l’amplitude des efforts.
Une autre composante de la difficulté de contrôle est illustrée par le cas du portique où le mouvement d’une masse déportée (le chariot ou la poutre) est déphasé avec celui donné par l’opérateur. Ceci se traduit par un modèle d’impédance d’ordre 3 et des constantes de temps associées[22].
Le frottement statique est source de difficulté de contrôle. Toutefois dans les systèmes que nous avons testés, le frottement statique n’était qu’une composante mineure, voire négligeable.
La compliance (souplesse) du système peut suffire à effectuer des petits déplacements avec un minimum d’effort. La compliance peut ainsi aider une opération d’insertion. Mais dans le cas d’un système libre, il prendra une nouvelle position d’équilibre quand l’opérateur le lâche, ce qui peut poser un problème de précision[23].
Enfin, la manipulation à deux mains souvent utilisée pour des opérations précises introduit une complexité supplémentaire si l’on veut mesurer en conditions représentatives.
Une alternative à une approche basée modèle est la réalisation de tests de dextérité[24] par des opérateurs, méthode qui demande des tests normalisés mais significatifs et la répétition des tests par un nombre suffisant de personnes.
Disposer d’un kit de mesure
Les systèmes de mesure prototypés au cours du projet et les traitements associés ne sont pas industrialisés à ce jour. Les industriels utilisateurs sont particulièrement intéressés par le système de mesure mobile, permettant aux ergonomes d’évaluer objectivement les efforts de manipulation sur les moyens installés. Les partenaires et le CEA-List sont ouvert à manifestation d’intérêt pour transférer l’expertise auprès d’une société qui serait intéressée à proposer un service ou un kit de mesure.
[1] Dans l’article ‘Is my cobot a robot or a loadhandling device ? ‘(Case Story COVR, 2021) Sylvain Acoulon aborde la question des différentes normes applicables suivant que le système est considéré comme un engin de lavage ou un robot industriel.
[2] Voir par exemple ‘Guide pratique d’ergonomie en conception industrielle/Practical guide to ergonomices in industrial design’, Jean-Francois Thibault (sous la direction de / edited by), bilingue, Octares Editions, 2017].
[3] Dans le cadre de l’évaluation des efforts de tirer- pousser lors de l’utilisation de chariot de manutention, l’INRS a montré que mesurer la force selon la seule direction de déplacement conduit à sous-estimer de façon importante l’effort [‘Les efforts de tirer-pousser – points de repère’, K. Desbrosses and al., INRS, ND 2365, Hygiène et sécurité du travail-3e trimestre 2012].
[4] L’évaluation du guidage manuel a été abordé récemment par le laboratoire de Robotique de l’université de Munich [Kirschner, R. J. et al. Manual Maneuverability: Metrics for Analysing and Benchmarking Kinesthetic Robot Guidance », in 2022 IEEE/RSJ International Conference on Intelligent Robots and Systems (IROS), Nov. 2022].
[5] « What constitutes an “ideal” telemanipulator? Intuitively a reasonable response would be: An ideal telemanipulator is one that provides complete transparency of the interface. In other word the operator feels as if the task object were being handled directly. » extrait de [G. J. Raju, G. C. Verghese, and T. B. Sheridan, “Design issues in 2-port network models of bilateral remote manipulation,” in 1989 International Conference on Robotics and Automation Proceedings, 1989, pp. 1316–1321 vol.3].
[6] Le terme d’impédance vient du domaine de l’ingénierie électrique et a été repris en mécanique acoustique et en robotique. Son origine est le verbe anglais «impede» qui traduit bien dans un contexte de mouvement une entrave ou un freinage. Il est le plus souvent utilisé dans un contexte de modèle linéarisé comme une fonction de transfert . Ce sont les travaux de Neville Hogan qui ont introduit ce terme dans le domaine du contrôle moteur humain et dans celui de la commande des robots. On trouve de nombreux travaux qui portent sur l’identification de l’impédance du bras humain lors de tâches simples.
[7] [T. Flash and N. Hogan, “The coordination of arm movements: an experimentally confirmed mathematical model,” J. Neurosci., vol. 5, no. 7, pp. 1688–1703, Jul. 1985].
[8] Dans le cas d’un déplacement sur une distance assez longue, la trajectoire type incorpore une phase à vitesse constante qui correspond à une phase de marche.
[9] On demande des aller-retour soit avec arrêt (brusques), soit continus (plus fluide) en modulant la vitesse. Avoir des dynamiques différentes permet une meilleure qualité d’identification.
[10] Dans le cas du dispositif mobile, la vitesse est obtenue par intégration de l’accélération libre et la dérive est corrigée en exploitant le fait que chaque mesure commence et termine à vitesse nulle.
[11] plus particulièrement dans ce cas des réducteurs «Harmonic Drive».
[12] La charge va s’ajouter à la masse apparente du système et le niveau de frottement augmente généralement avec la charge.
[13] Dans nos essais, c’était le cas des robots « collaboratifs » qui étaient polyarticulés et du bras d’assistance. Dans le cas d’un système articulé, les phénomènes physiques d’inertie et de frottement étant localisés au niveau des axes et des corps en mouvement, l’impédance apparente sera dépendante de la configuration des axes et de la direction du mouvement. Dans le cas d’un système à mouvement cartésien (XY, ou XYZ) seule la direction du mouvement est importante et non la position de chaque axe.
[14] Par exemple, dans le mode «guidage manuel» d’un robot, il n’est pas neutre de bloquer des axes de mouvement cartésien (fonction offerte par certains constructeurs). Les paramètres déclarés de masse de l’outil peuvent aussi influer.
[15] La variabilité dans les essais est réduite au final en les répétant et en les combinant dans la résolution numérique.
[16] L’effort prédit par le modèle à deux masses dépend du déphasage entre le mouvement des deux masses. Un majorant de l’effort est obtenu avec l’hypothèse d’une mise en phase des deux mouvements.
[17] Corresponds à l’indice de transparence proposé par Métillon pour la caractérisation de systèmes à câbles suspendus. Dans ce type de système inertie et frottements sont très faibles de sorte que le défaut de transparence est principalement cette anisotropie [Métillon, M., Charron, C., Subrin, K., Caro, S. «Stiffness and Transparency of a Collaborative Cable-Driven Parallel Robot». in Advances in Robot Kinematics 2022. ARK 2022. Springer Proceedings in Advanced Robotics, vol 24. Springer, 2022] [Métillon.M., Modelling, Control and Performance Analysis of Cable-Driven Parallel Cobots. Thèse de doctorat, École centrale de Nantes, Juin 2023].
[18] Corresponds aussi au critère assez improprement appelé “Motion steadiness” proposé par [Kirchner&al. 2022, déjà cité].
[19] Le protocole proposé par [Kirchner&al. 2022, déjà cité] utilise un tracker laser pour mesurer la direction du mouvement obtenue sous la sollicitation d’une force pure. Dans le cas d’un robot il serait possible d’utiliser la mesure de la position, sous réserve de calibrer la direction d’application de la force dans le repère du robot.
[20] Notre dispositif de mesure mobile ne permet pas d’obtenir une précision suffisante sur les déplacements.
[21] La force initiale (de démarrage) et celle d’arrêt (de freinage) dépendent de l’accélération mais aussi de la vitesse selon les paramètres dominant du modèle d’impédance. La force de maintien (ou de roulage) dépend de la vitesse. Ces forces sont définies dans la norme française [NF X35-109: 2011, Ergonomie – Manutention manuelle de charge pour soulever, déplacer et pousser/tirer – Méthodologie d’analyse et valeurs seuils, Octobre 2011].
[22] La difficulté de contrôle peut être abordée en considérant que l’opérateur régule sa force pour obtenir le déplacement ou la vitesse qu’il souhaite et en analysant le problème comme celui d’une synthèse de régulateur. Même si on ne peut pas assimiler le contrôle humain à un contrôle automatique qui plus est linéaire, on peut faire l’hypothèse d’une certaine conservation de la difficulté intrinsèque d’un système à être contrôlé. Une telle approche a été développée notamment dans des études cherchant à modéliser le comportement de pilotes d’avion. On en trouvera un aperçu dans l’article [Scibilia, A., Pedrocchi, N. & Fortuna, L. Human Control Model Estimation in Physical Human–Machine Interaction: A Survey. Sensors 22, 1732, Feb. 2022].
[23] Par exemple dans le cas de l’apprentissage de points par un robot en mode manuel.
[24] On trouvera un exemple de test de dextérité en télé-opération dans [David, O. et al. Digital assistances in remote operations for ITER test blanket system replacement: An experimental validation. Fusion Engineering and Design 188, 113425, March 2023].
Auteur : Catherine BIDARD, Chef de projet METRAMM, CEA-List